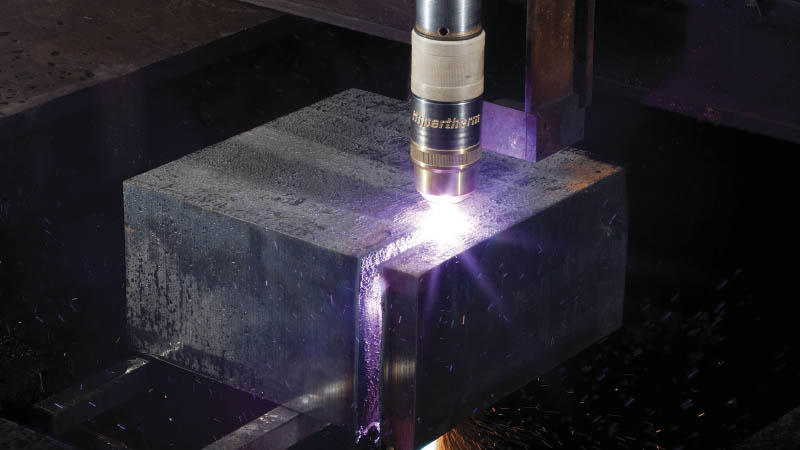
Ответ на этот вопрос можно начать с констатации факта, что в современном мире довольно мало абсолютно универсальных вещей. Данное мнение применимо и к существующим методам резка листового металла.
Область применения плазменной резки довольно широка, поскольку позволяет производить резку практически всех сталей и сплавов, а также алюминия и других токопроводящих материалов с достаточно высоким качеством. Метод основан на разделении материалов с помощью плазменной струи, генерируемой плазмотроном, температура которой достигает 20000oС, что позволяет производить резку на достаточно высоких скоростях до 25 м/мин. Диапазон толщин, обрабатываемых с помощью плазменной резки от 0,5 до 160 мм. Но, как правило, экономическая целесообразность применения данного метода находится в диапазоне толщин от 1 до 32 мм. Таким образом, плазменная резка это один из наиболее распространенных методов фасонного раскроя листовых материалов, а также труб и профилей.
Помимо вышеперечисленных фактов применительно к технологии плазменной резки вообще, следует сказать, что плазменная резка довольно гибкий инструмент и представлен на сегодняшний день как минимум тремя доступными технологиями:
- разделительная технология воздушно-плазменной резки;
- кислородно-плазменная резка;
- узкоструйная (высокотехнологичная резка).
Каждая технология имеет свою область применения и может быть использована для решения определенного перечня задач.
Воздушно-плазменная технология плазменной резки
Воздушно-плазменная технология плазменной резки - это младшая и наиболее дешевая из методов резки. При данном способе резки в качестве плазмообразующего и защитного газа используется только воздух. Более прогрессивные технологии резки предполагают применение более совершенных конструкций плазменных резаков и дополнительных технических газов. Это позволяет получать более высокие показатели конечного результата.
В тоже время плазменная технология предоставляет конечному потребителю дополнительную гибкость. Она заключается в возможности выбора оптимальной плазменной технологии как с точки зрения бюджета на внедрение нового оборудования так и показателей качества, которыми характеризуются различные плазменные технологии.
Нужно отметить что в настоящий качество термических способов резки принято оценивать по трем показателям:
- Конусности или косины реза;
- Шероховатостью;
- Допусками на геометрические отклонения детали.
- Система плазменной резки.
Еще один момент, который позволит понять причины популярности метода плазменной резки металла - это диапазон толщин сортамента листового металла, который используется в производстве металлоконструкций и различного технологического оборудования. В большинстве своем он находится в диапазоне от 3 до 50мм. А это именно те толщины на которых максимально раскрываются свойства плазменных технологий: качество и скорость резки.
Довольно часто на станках плазменной резки применяют комбинированный подход к производству станков. На одной машине размещают плазменный и газовый резак. И в этом случае толщины металла до 50 мм обрабатываем с помощью плазмы, используя все его преимущества. А металл толщинами 50-150мм обрабатывают с помощью газовой резки. Именно этот диапазон является основной областью применения газовой резки.
Автогенная термическая резка
Автогенная термическая резка получила широкое распространение в различных отраслях промышленности благодаря низким эксплуатационным затратам и своей простоте. Метод газокислородной (ав- тогенной) резки основан на разогреве металла до температуры плавления посредством горения смеси кислорода и горючего газа (чаще пропана или ацетилена) и горении металла при подаче в зону резки струи режущего кислорода. В промышленности, как правило, автогенная резка применяется для резки «черных» сталей толщиной до 300 мм. К преимуществу данного метода необходимо отнести отсутствие конусности, в то время как недостатками являются: невысокая скорость резки и относительно большая зона термического влияния. Но следует отметить что при резке металлов возникают и задачи, для решения которых следует прибегать к помощи других распространенных технологий.
Гидроабразивная резка
Гидроабразивная резка - способ резки, который отличается минимальными тепловложениями. Суть этого метода заключается в резке струей воды под высоким давлением, генерируемым насосами различной мощности с подачей в зону резки гранатового песка. Универсальность данного метода резки выражена возможностью решения широкого спектра задач, связанных с разделением самых разнообразных материалов: титановых сплавов, высокопрочных керамик и сталей, композитных материалов, полиуретана, поролона, пластмассы и многих других. Толщина резки гидроабразивом достигает 300 мм в машинах в стандартном оснащении. Отличительные особенности гидроабразивной резки – высокое качество при относительно невысоких скоростях.
Технология лазерной резки
Технология лазерной резки благодаря сфокусированному лазерному излучению, позволяет резать практически любые металлы и сплавы независимо от их теплофизических свойств. При этом можно получать узкие разрезы с минимальной зоной термического влияния и максимальной точностью. Лазерная резка предназначена главным образом для высокоскоростного раскроя тонколистовых материалов в диапазоне толщин от 0,5 до 12 мм. Конечно с применением лазерной резки есть возможность обрабатывать и большие толщины. Но данное оборудование довольно дорого, поэтому его применение ограничено среди широкой массы предприятий.
В заключении следует отметить, что именно плазменный раскрой металла является наиболее гибким и доступным инструментом. Более того именно метод плазменной резки наиболее эффективно способен решать задачи по резке наиболее распространенных толщин металлов с небольшими эксплуатационными затратами. И главный показатель, который заставляет делать выбор в сторону данного метода - это высокие скорости плазменной резки типичных толщин. А это гарантия высокой производительности заготовительного производства современного предприятия.